What Is Lean?
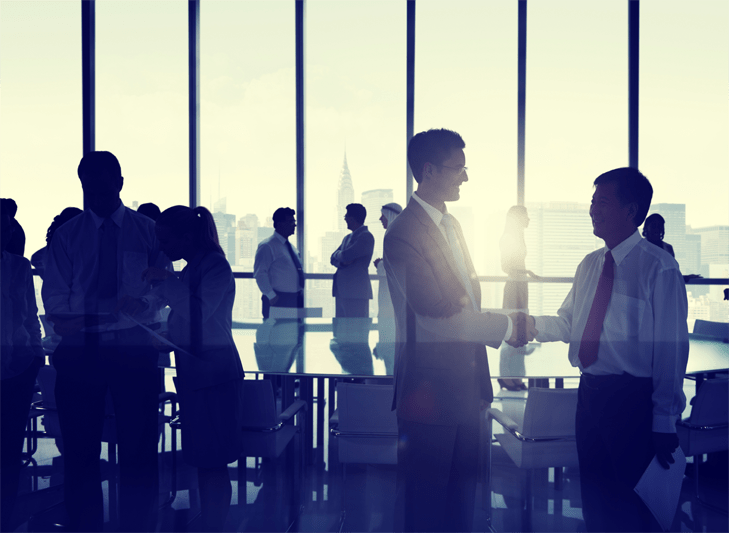
Management guru Peter Drucker said, “There’s nothing so useless as doing efficiently that which should not be done at all.” Lean is an improvement and problem solving methodology that strives to reduce or eliminate activities that don’t add value to the customer.
Lean is founded on two pillars: respect for people and continuous improvement. According to Dr. Shigeo Shingo, a Toyota engineer and expert on the methodology, Lean is a never-ending elimination of waste; it is committed to total customer satisfaction, total commitment to quality and total employee involvement.
An industrial engineer at Toyota, Taiichi Ohno, first developed the Lean methodology in the 1950s, then known as the Toyota Production System. One of the system’s major innovations is that workers were seen as problem solvers who are trained and empowered to improve their processes and eliminate waste.
Since the 1950s, the Lean methodology has made great strides in improving business performance across both manufacturing and transactional environments.
The Five Principles of Lean
Lean is much more than just a set of problem-solving tools. It was based on a foundation of principles designed to not only quantify and eliminate waste, but also help companies change the way they do business for the better. The following are five foundational principles of Lean and how they work together.
- Value—Understanding what the customer is willing to pay for. Value is always defined by the customer and is categorized in three ways: non-value add activity (waste), value add activity, and business value add activity.
- Value stream mapping—Mapping the process, steps, or sequence that a product or service goes through in a company.
- Flow—Allowing product and information requests to flow smoothly through the business without delay or disruption.
- Pull—Replacing only material that is used and eliminating excessive inventory, which allows us to respond quickly to customer requirements.
- Strive for perfection—Always striving to eliminate waste and improve the value provided to customers.
Understanding Value
In Lean terms, value is always defined by the customer, and there are three ways to categorize value: 1) Non-value add activity, known as waste, or muda in Japanese. 2) Value-add activities, which are essential, and 3) business non-value add activities, which are things that must be completed but don’t add value to the customer, such as meeting regulatory requirements.
To help determine if a process is value-add, Lean experts have developed a simple flowchart of questions. If the answer to all three of these questions is “yes,” then the process or process steps are value-add.
- Is the customer willing to pay for the good or the service?
- Does the step transform the good or service?
- Is the action done for the first time, or is it done many times?
Eliminating Waste
A key tenet of Lean is the reduction of waste. Using the acronym WORMPIIT, here’s a look at the eight types of waste that can be eliminated by using Lean techniques.
WORMPIIT: The Eight Types of Waste | |
---|---|
Waiting | Waiting for parts or information, e.g., an absence of flow, or a delay in the process. The goal is to be able to respond to the customer’s request with no delays to services or goods. |
Overproduction | Producing too much or too soon, i.e., to forecast rather than demand. This consumes resources with things the customer does not need and has not asked for. |
Re-work | Any repair or change to the product after it’s been made. One of the primary components of Lean is value, and something is only valuable if it was done right the first time. |
Motion | Actual movement of a person, e.g., unnecessary motion within a workstation or motion in a job task that takes too much time to complete. |
Processing | Over-processing of information, e.g., doing operations that the customer does not care about or does not ask for. |
Inventory | Any type of supplies and materials that are kept in a quantity above the minimum to get the job done. Inventory ties up financial resources and contributes negatively to quality issues. |
Intellect | Any failure to utilize the time and the talents of people, e.g., micromanaging and not empowering employees, or overlooking the collective knowledge of employees. |
Transportation | Any conveyance of a product, e.g., assembly lines, shipping and email. Transportation does not transform the good or service, it just simply moves it. |
Roles and Responsibilities
Within a Lean program, there are a handful of important roles. Here’s an overview of those roles and the responsibility and associated training of each.
Lean Masters
Lean Masters are expert leaders of Lean efforts, driving the organization toward the future state. They work with the core team and champions to manage Lean efforts, including developing training material, instructing Lean Leaders and practitioners, and mentoring projects. Lean Masters also help manage the project pipeline and lead larger scoped projects. Not only are Lean Masters very knowledgeable on methodology and application, they’re also seen as leaders in their organization and gain exposure across the company.
Training: Lean Master Development Program
Lean Leaders
Lean Leaders, also known as Lean Facilitators, are skilled practitioners of the Lean methodology. They are ideally dedicated full-time to leading SCORE events and other improvement projects. Executing four to six projects a year, Lean Leaders are experts in applying Lean tools and principles to reduce waste, improve processes, gain efficiency and boost productivity. Additionally, Lean Leader certification is seen as a personal and professional development building block that prepares people for leadership roles later on.
Training: Students should start with the Lean Practitioner course and progress through advanced Lean courses – please inquire
Lean Practitioners
These part-time resources carry the language of Lean deeper into the organization. They support and sometimes lead smaller scale projects, and also assist Lean Leaders and Lean Masters with team activities and tool application. Lean Practitioners become local advocates for continuous improvement and problem solving, and accelerate number of employees positively affected by Lean.
Training: Lean Practitioner Certification course
Process Owners and Team Members
Process Owners and Team Members assist with projects and tool application, as well as the implementation and continued control of improvements. They are also involved with culture change at a local level, as well as with project identification and execution.
Training: Lean Concepts and Tools Online
Certified Scrum Master – Agile
Scrum Masters facilitate a team that is using the Scrum approach to agile development. Originating in the IT world, this course is designed for any role at any organization. Scrum Masters are responsible for ensuring communication flows between the product owner and delivery team and for removing roadblocks and setting up processes for smooth workflow. When working with Agile, Scrum Masters also apply Lean tools and principles to remove waste from the development processes and requirements.
Training: Certified Scrum Master
The SCORE Roadmap for Kaizen Events
Sometimes known as “rapid improvement,” kaizen means “change for the better” in Japanese. Its essence is that change is good and good change is better. By this definition, anything a company does to make itself stronger is a Kaizen, and anyone who leads a Kaizen event in a company is a force for good change.
Change is good and good change is better.
Kaizen is a component of Lean that is designed to break down the project mentality of an organization and create a bias toward action. A Kaizen event is planned and structured and enables a group of associates to improve some aspect of their business quickly.
SCORE is a five-step methodology that provides the framework for managing and executing successful Kaizen events. Its five phases run in sequence and feed each other.
5 Phases of the SCORE Roadmap | |
---|---|
Select | Select the process(es) in need of improvement; determine who internally will be affected by the change, who should be involved in making it and how changes will affect customers; choose the tools and methods to address different performance issues. |
Clarify | Clarify the problem statement and the project objective; measure historical data to quantify current capability, including performance and waste; confirm Kaizen event team and training. |
Organize | Organize and train team members on the methods and scope; prepare the workplace, its suppliers, customers, facilities and people for the actual implementation of the improvement. |
Run | Execute the actual improvement event, typically lasting up to 5 days; it involves making observations, brainstorming and selecting improvements, and testing and implementing them. |
Evaluate | Evaluate the results and see the benefits achieved so far; gather feedback for standardizing new procedures, measuring return on investment and defining future work. |
Learn more about SCORE in this article on “Leading Lean Kaizen Improvements.”
Complementary Methods
While some companies deploy Lean solo, more often than not it is part of broader continuous improvement or performance excellence efforts that include Six Sigma, innovation, and other problem solving approaches.
Lean is often applied in conjunction with Six Sigma. Lean focuses on reducing waste so what is left is value-added. Six Sigma focuses on reducing variation and defects. Together, the two become a powerful combo to first lean out and then perfect your processes. In the last decade, companies have moved from treating Lean and Six Sigma as independent approaches to combining them into an improved operating system.
All of these continuous improvement efforts roll up into the organization’s strategic planning and execution, ensuring that everyone is working on improvements and innovations that align with the company’s strategic goals.
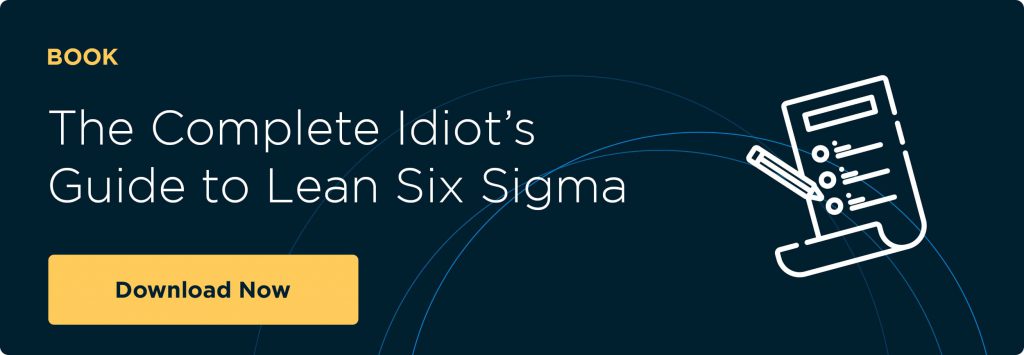