Smart Manufacturing
Welcome to the Fourth Industrial Revolution, where technology is now embedded within societies and even the human body. According to a November 2016 survey, approximately 75% of American own a smartphone and 92% of adults ages 18 to 29 own one. But it is not just smartphones defining this revolution, the Internet of Things (IoT) is turning everything from factory equipment and luggage to light bulbs and crock-pots into information givers and receivers.
Many digital systems, IoT in particular, can create value by combining sensor capabilities with systems that turn raw data into intelligence. IoT can also imply the ability to control mechanical systems remotely or autonomously. Once digitally connected, these systems capture and store vast amounts of data, enabling analytics to turn that data into actionable insight or enable value-added services not possible without Internet or equivalent connectivity. But are companies truly realizing the benefits of the digital age?
Challenges in Digital Adoption
Not unlike other data analytic initiatives, manufacturing companies are finding their number one challenge not to be technology, but acquiring the proper skill set. Studies from Accenture and PWC found that while investing in the right technologies is important, ultimately, success or failure is largely dependent on people-focused factors such as culture and clear leadership from the C-suite.
Many of these people-focused factors can be addressed by advanced planning. First, prior to digital implementation, it is vital to identify a clear definition of the strategy and desired outcomes. Without understanding the goal and what the environment will look like in the future, it is impossible to measure success. Once a clear strategy is in place, executives should perform a resource needs assessment to determine skill gaps and associated training requirements. An effective training plan can be developed based on the resource gap. Finally, create a saturation plan to ensure employees will keep up with industry trends and stay current with their new skills.
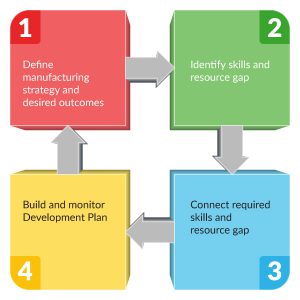
Using advanced planning to address people-focused factors
Strategy Creation
To be most successful, companies need to develop NOT a digital strategy, but a manufacturing strategy enabled by the digital generation. Don’t lose sight of the foundation of your business strategy. Focus on the outcomes the company desires and formulate a strategy accordingly. In addition, articulate key areas of investment and operational improvement required to deliver the desired business outcome. Then, carefully select the digital capabilities that can generate the improvement the company seeks.
Addressing the Skills Gap
After the company has outlined specific desired outcomes, a skills assessment should be performed. This analysis will clearly identify the strengths and shortcomings within the chosen team. Picking powerful performers in the organization with a proven track record is crucial when moving forward with digital adoption. These employees will be best poised for external training and ready to use new tools and skills to analyze data and gain valuable insight. Training should include methodologies around hypothesis generation, data analytic processes, tools, and data visualization and presentation skills. Following the training, employees need to ensure they have a saturation plan in place for continuous improvement of skills.
Digital Investment Goals
Many companies have lofty goals for their digital factory investments. We can categorize these goals into three groups: product, supply and machine. Data analytics and IoT systems can help with all three of these goals.
Within the product planning phase, factories that have embraced data intelligence can gain efficiency through standardization of methods, processes and information. IoT systems can improve product quality and reduce defects with virtual identification of product and process quality at an early stage. Quality assurance is important not just to the end user but also an integral part of the bottom line and operational expenses. Analytic insights can help improve product design and production. Manufacturers can also use data models to forecast output and demand. When factory data is combined with online behavior metrics, companies can determine correlations and provide insight into effectiveness of different campaigns for products and services.
Data analysis can also assist with supply chain planning and optimization. Tracking information and analysis will identify potential supplier components and part defects. The supply chain can become more efficient by optimizing data intelligence to adjust utilization, warehouse space and production planning. Data can also be analyzed to track the movement of vehicles and products to evaluate the costs of various transportation and process options. This real-time parts flow monitoring is the key to supply chain optimization.
Machinery itself can even be improved through intelligent use of data. For decades, manufacturers have used Lean and Six Sigma programs to reduce waste and variability in production. However, variability is inevitable in many areas of processing even after statistical techniques have been applied. Manufacturers are finding they need a more refined approach to diagnosing and correcting process flaws and data analytics is proving to be that approach. Operations managers can use analytics to optimize the variables that have the greatest effect on yield. With manufacturers across various industries having real-time data, they are aggregating data sets to uncover new insight into their operations. This real-time data also allows for immediate testing and simulation of new processes, as well as support for new mass-customization of improvements. By quantifying daily production, management has insight into how the machine impacts financial performance.
The End in Mind
In order to fully harness the power of the new digital revolution, organizations need to create a manufacturing strategy that’s informed and enabled by a new generation of data. What are the primary business outcomes the company desires? Focus on those and determine the digital capabilities required to achieve them. Remember the people-based components of the strategy. Provide appropriate training to the stakeholders and involve the C-suite in the communication and training. By keeping these outcomes and people in mind, a digital factory can ensure the data investment pays off.
Resources
- Rasmus, R. & Nichols, J. (2016). Digital factory: Cracking the code to success. Retrieved from https://www.accenture.com.
- Geissbauer, R., Vedso, J. & Schrauf, S. (2016). Industry 4.0: Building the digital enterprise. Retrieved from https://www.pwc.com.
- 4 Big Data Use Cases in the Manufacturing Industry. Retrieved from http://www.ingrammicroadvisor.com.
- Manufacturing Use Cases. Retrieved from https://mapr.com.
- Buvat, J., KVJ, S., Morel, V., Spitzer, B. (2013). The Digital Talent Gap: Developing Skills for Today’s Digital Organizations. Retrieved from https://capgemini.com.
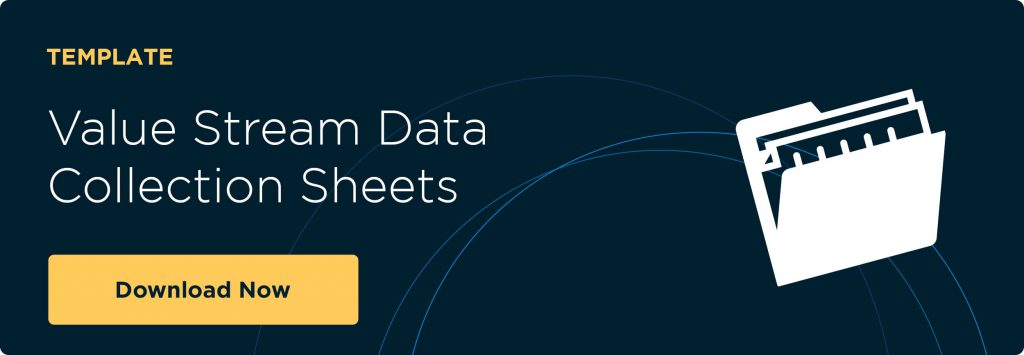